Focalizzarsi sui processi per realizzare il business model
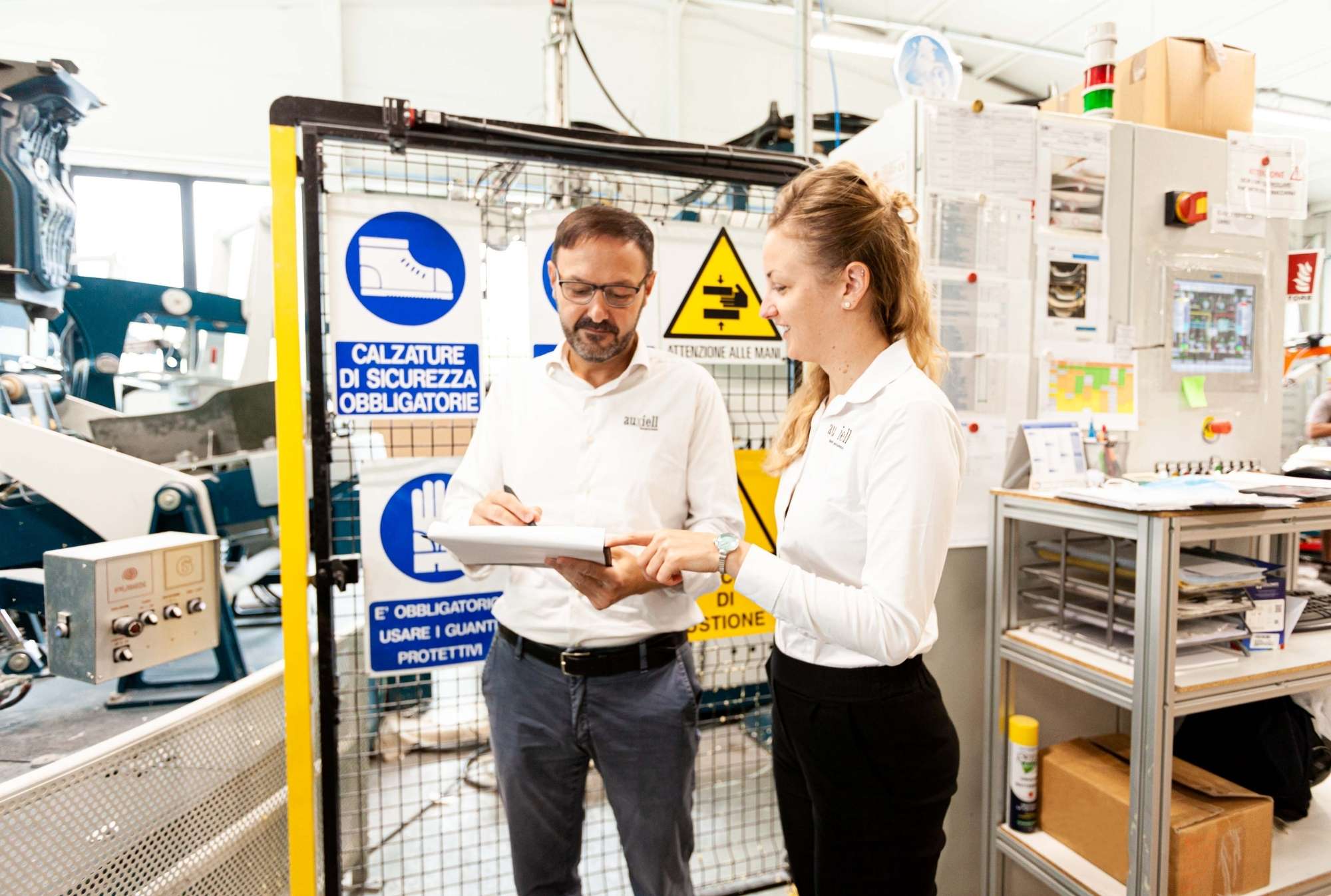
Enrico Franzolin
Inventor & Unox President
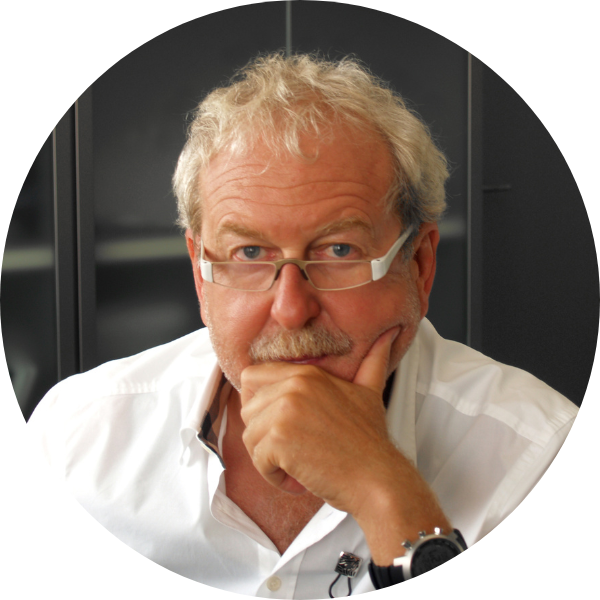
Quando nei primi anni 2000 Enrico Franzolin rileva l’intera proprietà di Unox, ha già chiaro in mente il modello di business, ma è alla ricerca di un sistema impresa che riesca a scaricare a terra le sue idee. Il sogno è diventato realtà grazie a Lean System, che con la sua applicazione trasversale a prodotti, processi e persone è diventato il principale asset organizzativo e di sviluppo dell’azienda. A sua volta il modello di business è cambiato, andando a evolvere di pari passo ai miglioramenti che avvenivano in azienda.
Si potrebbe sintetizzare così la trasformazione che ha coinvolto Unox ormai vent’anni fa e che con il continuo contributo di Auxiell, società specializzata nella complete lean transformation, continua ancora oggi.
L’evoluzione di Unox
Unox irrompe nel mercato dei forni professionali affermandosi da subito come azienda innovatrice, grazie soprattutto a una nuova tecnologia che garantisce la diffusione uniforme dell’aria utilizzando un sistema a ventole multiple. Enrico Franzolin, oggi presidente della società, non è tra i fondatori di Unox, ma vi entra quasi subito come socio e innovatore.
A Vigodarzere, 16mila abitanti alle porte di Padova, sorge il primo stabilimento e, mentre la maggior parte delle imprese esternalizzava e delocalizzava le proprie attività produttive, Unox ha puntato su un sistema industriale locale verticalmente integrato.
Negli anni 2000 l’azienda cresce velocemente, grazie soprattutto al processo di internazionalizzazione, ma con la crescita aumenta anche la complessità, e nonostante l’impegno profuso per creare tanti modelli diversi, come ricorda lo stesso Franzolin, «avevo il magazzino pieno di forni, ma ne mancava sempre uno per completare il camion». Un giorno, un dipendente gli parla di un libro che descrive un nuovo modello produttivo che non prevede scorte. È scritto da Shigeo Shingo, un consulente dell’azienda automobilistica giapponese Toyota, e descrive l’applicazione, in quello che nel tempo è divenuto il primo produttore al mondo di veicoli, di quello che oggi descriviamo come lean system, un sistema di management ai tempi ancora poco conosciuto in Italia. Franzolin ne rimane affascinato e cerca dei consulenti che lo aiutino ad adottare questa nuova metodologia. Nasce a questo scopo Auxiell, guidata da due giovani ingegneri padovani: siamo nel 2005 e comincia la reale trasformazione di Unox.
Inizialmente le cose non sono facili, c’è chi si oppone alla novità e al cambiamento, ma l’imprenditore insiste e un po’ alla volta i dipendenti capiscono che bisogna cambiare i processi produttivi, a partire dall’assemblaggio.
C’è un episodio in particolare che segna lo spartiacque tra la vecchia Unox e quella che vediamo oggi ed è la dismissione della macchina simbolo del vecchio modo di produrre, un sistema punzonatrice e pannellatrice con magazzino automatico ad alta produzione. Questa soluzione, che era ideale per produrre grandi lotti dello stesso pezzo, aveva però lunghi tempi di attrezzaggio tra un modello e l’altro. Con il nuovo approccio viene letteralmente smantellata perché non risponde alle richieste di efficienza di flusso. Al suo posto vengono inserite una serie di macchinari più piccoli e flessibili che fanno scorrere velocemente il prodotto all’interno della fabbrica, diminuendo le scorte in magazzino.
A monte il cambiamento raggiunge anche i fornitori a cui viene chiesto di produrre tanti piccoli lotti, ma non tutti riescono a soddisfare queste nuove esigenze. Anziché cercare nuovi fornitori, Franzolin decide di internalizzare la supply chain creando nuovi stabilimenti: è la genesi di Velex, Mabix, Detix e Esse3 che vanno a integrare la catena produttiva, permettendo il controllo dell’intero processo. Attualmente oltre il 90% dei pezzi che compongono i forni Unox vengono prodotti all’interno del gruppo, in società perfettamente integrate nei processi e in grado di assicurare una produzione just in time che permette di ottimizzando la gestione delle scorte.
Questo ha reso Unox meno vulnerabile alla crisi di forniture che oggi sta colpendo le aziende europee. Come è solito ripetere il presidente Franzolin, «preferisco avere 3 milioni di euro investiti in macchinari anche fermi che 3 milioni di scorte in magazzino, perché queste ultime hanno un costo di gestione che non voglio pagare».
In vent’anni, questa trasformazione ha portato i tempi di produzione dal ricevimento dell’ordine dai due mesi alle quattro ore attuali, mentre le rotazioni di magazzino del prodotto finito sono aumentate clamorosamente da 5 a oltre 70. Il fatturato raddoppia ogni 5 anni come previsto dal business plan, mentre il magazzino continua a rimanere pressoché invariato.
Ma torniamo al 2009. Visti i risultati positivi, Unox decide di adottare il lean system anche per gli altri processi dell’azienda, come la progettazione del prodotto e le vendite.
Grande attenzione viene posta ai processi di vendita perché ci si accorge di non conoscere sufficientemente il cliente finale, con cui la società non ha contatti diretti e di cui non percepisce i bisogni effettivi.
Si decide così di andare a parlare direttamente all’acquirente finale (in accordo con i distributori) creando la figura dell’Active Marketing Chef, uno specialista della cucina in grado di dialogare con ristoratori e cuochi cogliendone le istanze e risolvendo contemporaneamente dubbi e problemi. Questa figura combina un cuoco, un tecnico e un venditore. Il nuovo incaricato si presenta dal potenziale cliente dando la possibilità di provare con mano i forni nella propria cucina e con le proprie ricette. L’idea si rivela talmente vincente che il tasso di conversione in vendita è altissimo.
Per quanto riguarda il processo di sviluppo dei nuovi prodotti, Unox ha creato team multidisciplinari che combina ingegneri di vario tipo, dai chimici, ai meccanici agli aerospaziali. In questo modo le competenze si combinano e nascono nuove tecnologie. Questi esempi rappresentano perfettamente l’idea di Unox sulla people strategy. Abbinare processi eccellenti con talenti che vengono inseriti e formati nel miglior contesto lavorativo possibile per arrivare sempre a risultati eccellenti.
Ora il sogno è Unox City, la nuova fabbrica. Qui si andrà a riprogettare il flusso produttivo ottimizzandolo ulteriormente, con l'obiettivo di arrivare al “one piece flow” perfetto. I lavori sono già iniziati e porteranno alla realizzazione di 60mila mq dedicati a produzione e logistica, 4mila mq destinati a ricerca e sviluppo, oltre a 2mila mq riservati ad aree relax e pausa pranzo. L’investimento totale al termine dei lavori supererà i 68 milioni di euro.
I vantaggi saranno notevoli, primo fra tutti si porteranno sotto lo stesso tetto la maggior parte delle attività della catena produttiva, riducendo ulteriormente il magazzino e i tempi di attesa. Inoltre, i nuovi spazi sono stati progettati con un occhio di riguardo al benessere dei dipendenti e alla sostenibilità.
«In tutti questi anni siamo stati al fianco di Unox - commenta Francesco Culòs, partner di Auxiell - lavorando per realizzare il sogno dell’imprenditore. Oggi l’azienda è diventata uno dei pochi esempi europei di trasformazione completa in chiave lean, un modello di riferimento di come dovrebbe essere organizzata una lean enterprise. Noi crediamo che l’esempio possa aiutare molte altre aziende a realizzare i loro sogni». Perché, come dice Franzolin, «Se io avessi avuto vent’anni fa una persona che mi avesse spiegato i principi e i metodi alla base delle scelte da fare, come faccio io adesso con altri imprenditori, avrei commesso meno errori e risparmiato tanta fatica».